Smart Valves: Key Considerations for Integrated Data Collection
Integrated sensors are a key tool for measuring data in fluid management. Characteristics of fluid flow such as temperature, pressure, and flow rate are critical for most applications, but they are not the only data points that can deliver valuable insights around performance and efficiency. Valves control the flow of fluid in different ways depending on the final system, so valve performance data such as vibration, position, or current/power usage can be important as well. This paper will review some of the most popular sensors being integrated into valves, their capabilities, and some important considerations for engineers.
SENSOR CAPABILITIES AND PERFORMANCE DATA
Measuring Fluid and Ambient Temperature
Temperature sensing is popular in fluid management, and fluid temperature is one of the most commonly collected data points. An integration plan that collects ambient temperature information in addition to fluid temperature can provide insight into system performance under changing conditions. In an electric vehicle application, using this data to modify cooling paths with control valves in the thermal management system can maintain the power module, motors, and battery pack within their optimal temperature parameters for efficient operation. Knowing the overall "state of health" of the vehicle's systems can extend range as well as lifespan by avoiding detrimental temperature extremes. Data collection of this type is also relevant in processing and manufacturing settings where the temperature may shift significantly with changing seasons or due to equipment issues. Understanding temperature’s impact on system operations can be instrumental in maximizing efficiency and uptime.
Temperature measurement technologies are useful, but they can have an impact on flow rates, pressure drop, and other areas, so it is important to keep in mind system requirements and the impact of measurement on performance.
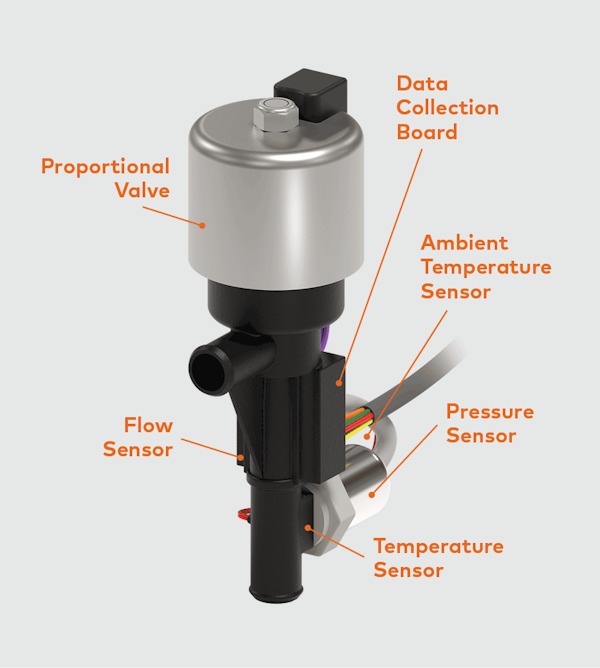
Gauging Shock/ Vibration with Accelerometers
Accelerometers can provide useful insights into operations, from documenting unexpected impact to providing notice of imminent equipment failure. However, it is important to understand what the sensor should be looking for, as requirements can vary depending on the application. For example, manufacturing or processing equipment will see some movement during operations from ongoing activities. A sharp increase in the accelerometer readings could be a sign of unexpected impact or an accident. In either case, operators should investigate the area of the equipment where the unusual reading was logged to see if there are any issues.
The positioning of the accelerometers and knowing how the valve will be used in the system are of particular importance. Accidental contact with any outside force will throw off readings, and environmental conditions can also influence data accuracy.
Tracking Current/Power Usage
Energy consumption data is another useful indicator of component and system health, especially when it can be evaluated against an optimal range. Many components are sized based on their power draw, so a shift in behavior can be significant. For example, an increase in energy consumption could be a sign there is an issue with the electrical connection and that not all of the power is making it to the actual component. This is not unusual, especially in equipment that has many moving parts or receives ongoing maintenance. Energy consumption data can help highlight issues before they become critical and increase the efficiency and effectiveness of system maintenance.
Tracking normal power usage over time can also be valuable, especially in larger systems where variations in usage can have significant cost implications. This data could also give insight on opportunity cost for future adjustments. For instance, a new subassembly could be proposed as a cost savings. Testing conducted with these sensors in place would enable engineers to confirm that production does not drop off and that the subassembly cost savings would not be lost in covering higher energy costs.
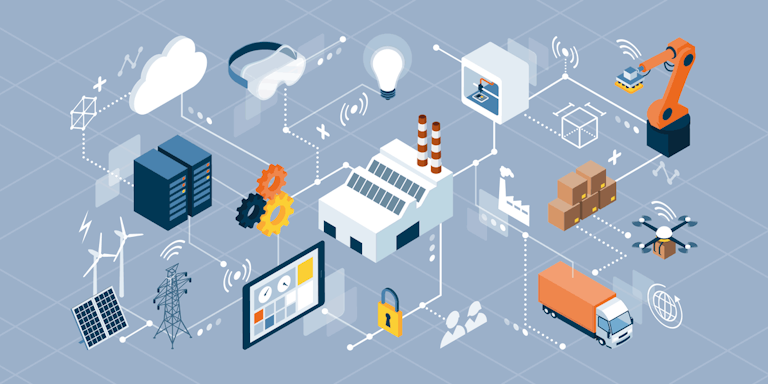
Detecting Leaks or Contaminants through Pressure Change
System leaks, contaminants, changes to fluid viscosity, and other issues can affect pressure and impact system performance. Pressure sensors can help confirm differences between the target pressure and actual pressure as well as help localize pressure loss. Data showing the differences between target and actual pressure highlights the presence of any issues that can lead to critical system failure if unaddressed. Targeting pressure changes in a large system goes a step farther, increasing maintenance efficiency by narrowing the search area for leaks, hose kinks, or other issues.
Maintaining Optimal Flow Rates
Optimal flow rates can vary widely by application, but the data can still be a valuable indicator of system health and performance. For example, a radical shift in flow rate would be a critical sign that there is a problem. A big drop in flow could be from a leak upstream or maybe some type of blockage that is limiting fluid throughput. Flow data collected at several points can help pinpoint problem areas.
ADDITIONAL CONSIDERATIONS FOR OEM PROJECTS
Aggregating and Sharing Sensor Data
The choice of methods used in gathering, sharing, and analyzing data collected from integrated sensors is an increasingly important consideration. Many OEMs are already including Internet of Things (IoT) infrastructure in their designs. In these cases, connectivity is not a challenge, but it is important to review how systems aggregate sensor data before sending it out. An aggregated approach is often easier than trying to manage different internet connections for each key component with integrated sensors. With that in mind, collecting the data locally can be done through wired connections or by implementing wireless communications. Beyond looking at how the data is moved, it is also relevant to consider whether encryption is needed either as a security precaution or for protection against future data legislation.
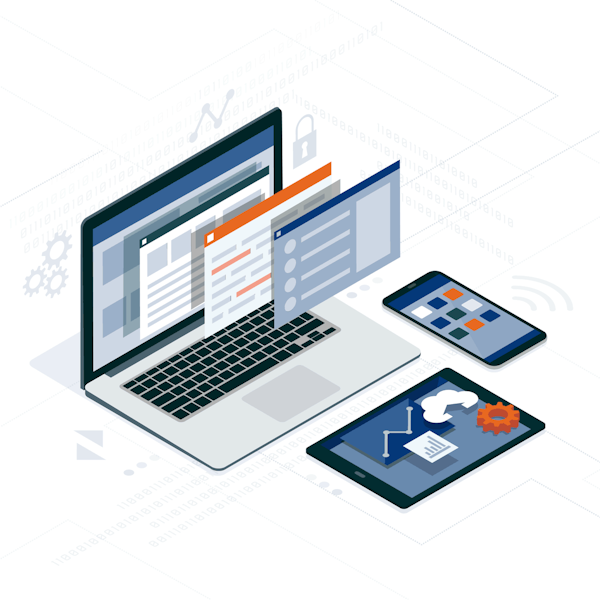
Preparing for Artificial Intelligence (AI)
Once sensors have been integrated into a valve design and internet connectivity has been applied to the product or system, the data can be transferred for further use. The development team can create their own monitoring system and/or provide an API so clients can import the data into their own system. An initial step for a proprietary solution could be to create a web dashboard that displays the current status and allows end customers to program optimal performance zones. If any parameters move outside of optimal areas, the dashboard can trigger an alert via text or email. Integrating reporting is another useful option. The dashboard can allow users to set up daily or weekly reports that track system level performance, components out of range, downtime, and other key metrics.
Data collected from integrated sensors can create even more value through the use of Artificial Intelligence (AI), but it is important to note that all information collected from sensors must be time/date stamped in order for AI to be effective. It is also important that a data structuring standard be implemented to make sure the output from all of the sensors has the same format. Even though most design engineers will not be involved in creating the database or AI systems, they should understand how intelligently integrated sensors can increase the value of the end product.
Conclusion
The use of sensors in OEM products and systems is becoming much more common. The integration of sensing into key components like valves is the next key advancement. Integrated sensing can help organizations track performance, increase uptime, and simplify maintenance. Data from integrated sensing makes it easier to leverage the benefits of monitoring systems and AI programs to track performance, identify patterns, simplify maintenance, and increase efficiency.
This article was originally published by TLX Technologies in January 2021
Want to explore design examples?
TLX Technologies is the go-to custom solenoid partner of the world’s top brands, first-tier suppliers, and OEMs