Latching Solenoid Fail-Safe
The current focus on energy efficiency has renewed interest in latching solenoid technology. Many electric vehicle applications need to be able to make the best use of every available joule, and any component that can minimize power consumption is highly desirable. While latching technology has been available for many years, it has suffered from one major drawback for vehicle applications: the lack of fail-safe functionality. If power is lost to the system, the solenoid would remain in its last commanded state. However, over the past few years, innovations with fail-safe (latch release) technology can now provide the necessary protection.
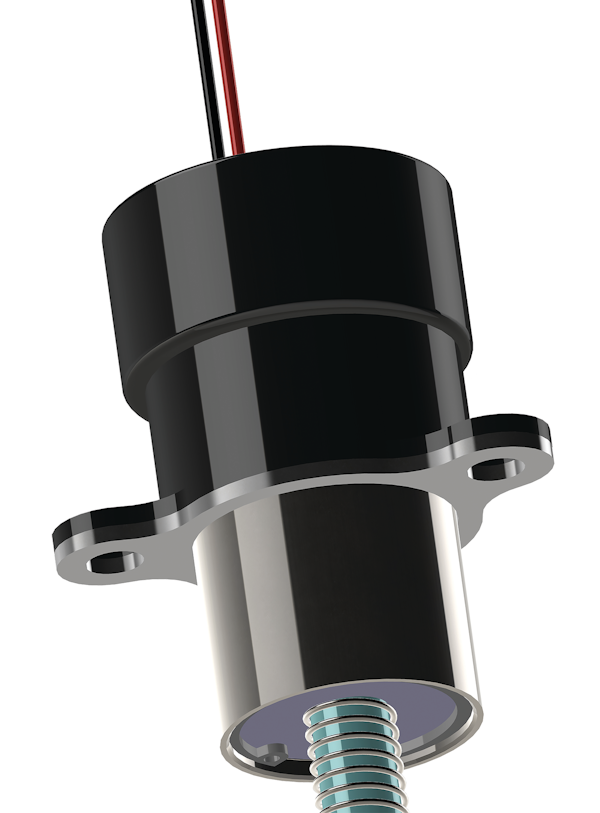
Latching solenoids are desirable where energy efficiency is a priority because they draw very little power. This makes them ideal for applications where high cycle rates are not needed. Only a short pulse of power is used to latch or de-latch the solenoid’s armature. A pulse of current of one polarity is used to actuate the armature, and either a permanent magnet or residual magnetism is used to hold the armature in position. A short pulse of current of the opposite polarity is used to release the armature.
By drawing so little power, they also generate very little heat. Design teams have at times shied away from taking advantage of these benefits because of the need for a fail-safe mode. As previously stated, without power, the solenoid cannot change state, and the armature will remain in the last commanded position if power is lost. This can be a significant safety concern if the last commanded position is not the same as the safe position.
Advances in technology have made incorporating a fail-safe control system into the solenoid design a reliable solution to this problem. The fail-safe is simply an integrated capacitive discharge circuit. When power is applied to the solenoid, the capacitor is charged in parallel. Even though the solenoid only requires a short pulse of power to change state, the capacitor continues to receive a constant voltage signal to maintain charge, but it draws nearly zero current. If power is lost to the capacitor, the capacitor discharges and moves the armature to the designated safe position.

The location of the fail-safe control can also be customized, as required by the application. One option is to locate the fail-safe on the solenoid’s power wires, but this has one significant disadvantage: If the wires are cut or damaged between the fail-safe control and the solenoid, the fail-safe will not function. The best and most reliable solution is to mount the fail-safe directly on the solenoid. This eliminates the possibility of loss of communication between the fail-safe and the solenoid should the power wires suffer damage.
There are numerous applications where latching solenoids equipped with a fail-safe control can be successfully used in vehicle applications. A latching solenoid valve in an EV thermal management system could be designed to actuate to a “limp home” valve position in the event of loss of power to the valve. A battery disconnect solenoid could be designed for EVs and HEVs to automatically cut power from the lithium-ion battery in the event of a collision to prevent accidental electrocution of vehicle occupants or first responders. Even if power is lost to the battery disconnect as a result of damage from the collision, the fail-safe would still actuate the solenoid, disconnecting the battery.
The advent of reliable fail-safe controls makes latching solenoids an ideal solution for vehicle applications with a low cycle rate. They draw very little power, and they generate very little heat. In the event of power loss, they can fail to a customizable safe position.
This article was originally published by Electric & Hybrid Vehicle Technology International in November 2021
Want to explore design examples?
TLX Technologies is the go-to custom solenoid partner of the world’s top brands, first-tier suppliers, and OEMs