Advanced NGV Valve
Rising fuel costs and increasingly stringent emissions standards have driven automotive manufacturers to greatly increase interest in alternative fuels. One such surge in alternative fuel development has been natural gas. The abundance, as well as the clean burning nature of natural gas, gives it the edge over gasoline and diesel engines in an industry pushing for environmentally friendly designs.
TLX Technologies has taken this opportunity to develop the next generation of shut-off valves for LNG vehicles. However, there are multiple challenges encountered when developing new technologies for LNG vehicles.
A major challenge associated with the design of LNG valves was sealing. The low temperature requirements (as low as -60°C) on their own are typically no problem for silicone or fluorosilicone elastomers. However, both of these materials lack the compatibility with natural gas to be viable with the low leakage requirements of the valve, as well as the strength and abrasion resistance required for dynamic seals. Currently, TLX Technologies uses a fluorocarbon elastomer specially designed for use in compressed natural gas vehicles for the valve’s dynamic seals. The FKM elastomer has been tested and shown to maintain its seal in temperatures as low as -40°C.
The low temperatures also posed a challenge in fitting system components. When energized, the coil of a solenoid can reach temperatures as high as 200°C. This, in combination with the extremely low temperatures of flowing natural gas, created large temperature gradients within the solenoid. Thanks to finite element analysis software, TLX Technologies studied this temperature variation in the solenoid and incorporated the corresponding thermal expansion into tolerance stack-ups. This was especially important where plastic components - such as an overmolded coil - mate with metal components, as plastics have coefficients of thermal expansion ranging from 3 to 10 times that of low-carbon steel. To reduce the effect of thermal expansion, the company utilized glass-fiber-impregnated plastic, which reduced the coefficient of thermal expansion, as well as giving a higher tensile strength than the unreinforced matrix material.
Other challenges met during development of the valve included meeting flow requirements. The valve system needed to be able to support a high mass flow rate across a large range of inlet pressures and temperatures while maintaining a pressure drop of less than 7psi. Low-pressure and high-temperature operating conditions were the primary focus during valve design. In these conditions, the valve is more likely to present its highest pressure drop and flow velocity. This is due to the decreased density of the fluid when compared with the high pressure or low temperature operating conditions.
To ensure an optimal valve design, the company used computational fluid dynamics software to observe flow characteristics of the valve. These characteristics included pressure drop between the inlet and outlet, flow paths, flow velocities, and Mach numbers. Variance in characteristics such as orifice sizes and locations often has a significant impact on this data.
Figure 1
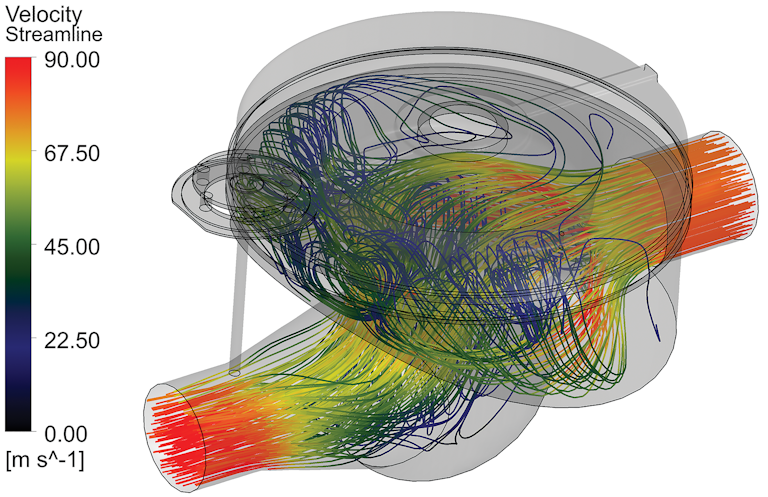
For instance, smaller flow areas can decrease overall size and cost of the valve, but increase flow velocity. If the flow velocity becomes too large, approximately 0.3Ma, the numerical model can become inaccurate since the flow is no longer considered incompressible. In addition, audible noise from the flow becomes more noticeable as flow velocity increases.
TLX Technologies is able to answer unique system demands with superior electromagnetic solutions. The company works with customers to design and develop solenoids and solenoid valves that meet the challenging requirements of automotive system applications.
This article was originally published by Engine Technology International in January 2019
Want to explore design examples?
TLX Technologies is the go-to custom solenoid partner of the world’s top brands, first-tier suppliers, and OEMs